Metal Injection Molding Process
- Firstly, metal powder particles and a binding agent are mixed to create a homogenised mixture. This is known as the Feedstock.
- Next, the Feedstock is injected into a mold cavity to form a Green Part, which is defined as a part made of powdered material that is compressed and held together with binding material. It then undergoes a binder removal process, through either heat or chemical treatment, to produce a Brown Part.
- After debinding, the Brown Part undergoes a sintering process at a specific temperature/atmosphere profile, until it hits the targeted density. It is then left to shrink up to 15%.
MIM Materials
In mixing, different metal powders are blended to form the alloy composite mix according to the customers' specific requirement. The Metal/ceramic powder is then mixed with wax and/or plastic materials (commonly known as a binder system) to form feedstock.
Our latest material list available here.
MIM Applications
Metal Injection molded parts have applications in various industries, due to their ability to be shaped in complex geometries.
Automotive
MIM is widely used in Automotive, Medical, Industrial & Consumer sectors, Semiconductor, Energy and in 5G Applications.
In the Automotive sector, MIM components are used to build sensors, engines, gearboxes, and many others systems requiring high strength and complexity.
Medical
In Medical applications, MIM is used mainly to manufacture surgical instruments as well as end effectors. A common material used is stainless steel due to this alloy having good strength, hardness, corrosion resistance, and good hygiene (i.e. easy to sterilise).
Consumer Electronics
In Consumer applications, MIM components need to be small-sized and complex with high volumes. Examples are components like SIM card Tray, connectors, hinges & camera mount frames.
MIM Design Guidelines
General Guidelines
Dimension Tolerances
Part Thickness Guidelines
MIM Advantages
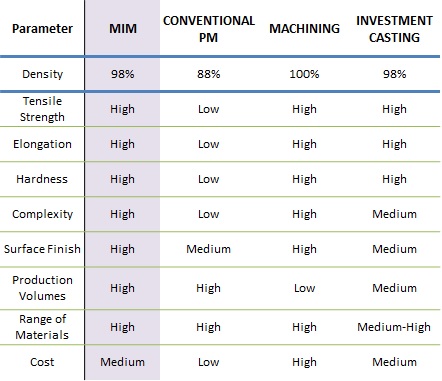
Some MIM Advantages are:
- Net shape production that minimises or eliminates machining.
- Ability to combine functions and eliminate sub-assemblies.
- Design flexibility for intricate and complex geometry.
- Good dimensional control with tolerances up to +/-0.3%.
- Thin wall capability of up to typically 0.30mm.
- Excellent material properties: density, mechanical strength, surface finish, magnetic properties, etc.
- Wide range of materials and customisation possible.
- Cost efficient for moderate to high volume production.
Discover MIM Manufacturing Solutions With Dou Yee Technologies
Metal Injection Molding (MIM) offers a powerful solution for producing intricate metal components with high precision, making it an essential process for industries like automotive, medical, and consumer electronics. The combination of design flexibility, material strength, and cost efficiency positions MIM as a top choice for manufacturers aiming to innovate and optimize their production lines.
Dou Yee Technologies has the manufacturing capability needed to provide advanced MIM solutions and take your production to the next level. Contact us today to find out more about what we offer.
Dou Yee Technologies provides services worldwide, including direct coverage in Singapore, Germany (Dusseldorf, Stuttgart, Frankfurt), and the US (California, North Carolina). We also extend our services to many other countries and regions across the globe. Contact us today to inquire about how we can assist you, wherever you are located!
Contact us today to inquire about our services.
Contact us today to learn more on our services rendered.
Contact Us